EI統合(Electric-instrument Integration)による人員/操業効率化 【PA分野】
EI統合(Electric-instrument Integration)による更なる省人化、計装=電気システム統合による省力化
ベテラン技術者の定年退職や、求人難等による人員不足に対応した新運転操業システムの構築省人化のために、製造現場システムの一体化と
更なる包括的な運転/操業システムを構築していく必要がある。その課題の克服のために今後目指すべきことは、現状の計装分野と電気分野の統合=EI統合(Electric-instrument
Integration)である。それを実現することで、全ての製造現場で電気と計装の両方を一括で運転/操作することが出来るようになり運転者の省人化、操業技能の集約化を進めることが出来るようになる。
この計装分野と電気分野の統合=EI統合を実現する為に、私どもは現状のDCSを主体とした計装システムから全く新しい計装制御システム"集中型制御システム:CCS"を構築することで、より簡単に実現できると考えている。
ハードウェア構成例
この新しい計装制御システムは分散型でなく、1台の”FTサーバ機(*1)”をメインハードウェアとして構成されている。
これを現状のDCS(分散型制御システム)と区別する為に、私どもは集中型制御システム(CCS:Concentrated Control System)と称し、略して”CCS”と呼ぶ。本ホームページでもこれ以降、この新しい計装制御システムをCCSと略す。この新しい計装制御システムの詳細については”CCS構築”のページで後述する。
CCS(新計装システム)のハードウェア構造はメイン制御部分と操作監視/上位通信部分をサーバ機(FTサーバ)で実現しており、”I/O(現場信号の入出力)部分”は”PLC”で構築されている。
よって、CCSでは計装制御システム部分(現”DCS”部分)と並列に設置されることの多い電気関連のPLCシステムとをオープンな”Net-Work”を使って簡単に接続することができる。
*1 FTサーバ(Fault Tolerance Server:フォールト・トレラント・サーバ)の略称
完全2重化の無停止サーバ機のこと
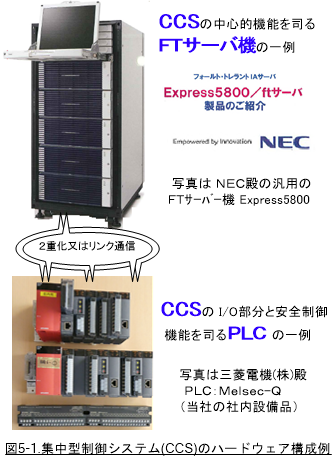
現状の計装システム(主に”DCS”)と電気関連システム(主に”PLC”)をシステム統合する場合
現状の計装システム(主に”DCS”)と電気関連システム(主に”PLC”)を”DCS計装システム側”にシステムを統合するには「図5-2」に示すように
DCSとPLCを”Ether-net”等の通信で繋ぎ、システム間のデータ通信ができるようにして実現するのが一般的と考える。具体的な実現手順を下記に示す。
① ”DCS”と”PLC”とを”Ether-net通信”等で接続し、DCS側に全てのPLC情報(例えばPLCの”全I/O情報”)を高速に通信できるようにしていく
② 電気関連の実際の制御部分をDCS側の制御機能(コントローラ内)に取り込んで”DCS機能”で実施していく
③ 計装側と電気側の両方の操作、監視(表示/操作ができ、さらに警報/ガイダンスなどの発報も行なえる)が同一の”HMI”:操作監視機能(”PC”等)の
同一モニタ上の同一画面で行なえるようにしていく
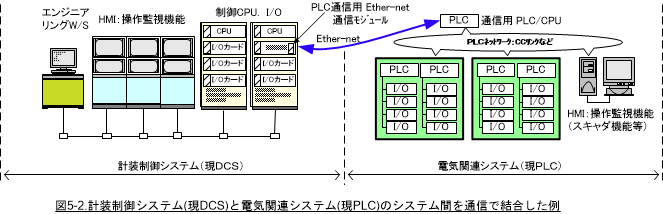
新しい計装システム(CCS)と電気関連システム(主にPLC)をシステム統合した場合
新計装システム(CCS)と電気関連システム(PLC)とを統合しようとすると、下記の処理が必要になる。
「図5-3」に"CCSのI/O部分のPLC"と”電気側PLC”とを一般的なPLCネットワーク通信の結合によって、両者をシステム統合する例を示す。
① CCSのI/Oネットワーク(2重化Ether-netやCC-Link、FL-net)とPLCシステム側のネットワークを接続する
② CCSは"メインサーバ機"部分と"自身のI/O部分であるPLC"部分とで構成されており、"電気側のPLC"とをPLCの標準的な通信機能で
直接接続することができる。CCSのメインサーバ機部分では、"自身のI/O部分であるPLC”と”電気側のPLC”の両方の"PLC"内の
レジスタ【原則B-レジ(”BITデータ”のレジスタ)、W-レジ(”Wordデータ”=アナログ信号データのレジスタ)】を
同等にCCS内でタグ化することができる。つまり、CCSの”I/O部分のPLC”と”電気側PLC”の全てのレジスタにタグ名、データタイプを付けることが
できるのである。CCS内のコントローラ部分(メインFT-サーバ機の制御用CPUユニット部分)はこの”タグNO.”を使ってコントローラ内の内部計器の
入出力定義やシーケンス処理(SFCやロジック処理)に必要な制御機能の定義を行える。
よってCCSでは “I/O系”が”PLC”でありながら現状の”DCS”の制御機能構築ビルダ並みの手順/方法で簡単に制御機能を構築することができる。
この様にCCS内の制御機能を使用し、電気側の制御機能をCCSの内部で実現することで、計装システム(CCS)と、電気関連システム(PLS)との
システム統合を実現することができる。
上記の計装システム(CCS)と、電気関連システム(PLC)とを”CCS側”に統合することにより下記のメリットが考えられる。
① 新たなネットワークシステムを組むことなく、既存のネットワークとの接続だけで通信ネットワークを構築できる。
しかも”PLC側”の標準的な通信機能をそのまま利用できる為、高速・大容量通信も可能で、原則的に通信系の2重化(リンクバックを含む)が
標準的に利用できる。
② ”CCS側”では”現DCS”と同等クラスの制御機能及び操作監視機能が実現されており、電気関連設備の運転監視で現状のDCSと同等クラスの
運転/操作が可能になる。これにより、いままで電気関連のPLCの操作監視に使っていたHMI(スキャダ等)が不要になる。
③ CCSで標準的に搭載される”PIMS(プロセス・インフォメーション・マネジメント・システム )機能”により、MES等の上位サーバ側で必要な
電気側の必要な全データを直接活用できるようになり、さらに全通信データを20年以上保持でき、過去のトレンド表示や帳票処理が極めて簡単に
実現できるようになる。
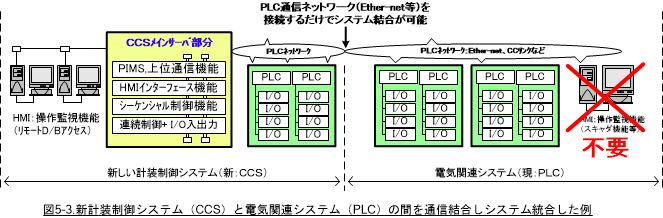
エッジコンピューティングによる戦略的経営支援+現場バックアップ運転 【FA分野】
FA分野での企業全体の生産/物流の最適化について
FA分野においては現場の生産ライン側を”エッジコンピューティング化"することで企業全体の統合管理システムを構築し、
これによって” 企業全体の生産/物流の最適化”が実現できると考えている。この”基本プラットホーム”の機能構成の概念を「図5-4」に示す。
現状、FA分野では 原則的にMES(工場管理システム)部分に各ライン内の各生産設備毎のPLC等のシステムが直接つながり生産ラインの操業/運転が
行われている場合が多い。
このためERP=MES=現場生産システム(PLC)を情報統合し、 企業全体での生産/物流の最適化を行おうとすると2つの克服すべき点があると考えている。
1. 企業全体の情報統合をしようとすると現場PLCの情報までを直接取り込む必要があり、情報が膨大になる
2. 企業全体の統合システムで直接運転する仕組みを現状のシステムのままで統合して構築すると、万が一の統合生産管理システムの不具合発生時、
現場の各生産ライン毎のバックアップ運転の機能が脆弱になっている。
上記の脆弱性を改善するために、下記の様な"エッジコンピューティングシステム"の構築を提案していければと思う。
1.に対して ⇒ エッジコンピューティングの概念を確立できるように、各工程ごとの機能を1つの系列の生産ライン全体で
1つにまとめた運転制御システム(”PA分野”の”DCS的なシステム”) を導入することで解決できると考えている。
2.に対して ⇒ 1系列の生産ライン全体を運転/操業ができるような完全2重化の運転制御システム(”PA分野”の”DCS的なシステム”)を導入
することで、上位のシステムやその通信系で何かしらの問題が起きても、各生産ラインごとで確実な現場運転/操業ができる。
このような”FA生産システム”を導入している生産現場向けに、私どもは エッジコンピューティングの概念を導入し、また1系列の生産ライン全体を
バックアップ運転できるシステムとして”CCS"(*3)を提案していければと考えている。
*3:新計装システムを集中型制御システム(CCS:Concentrated Control System、”CCS構成”の章で後述)
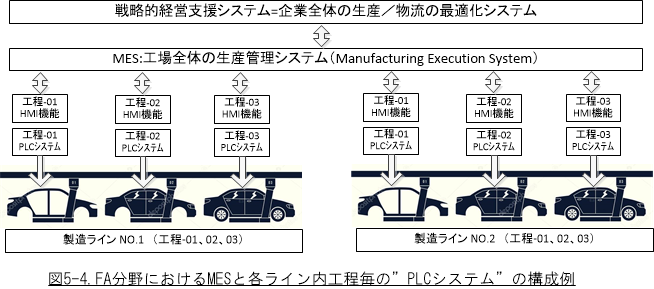
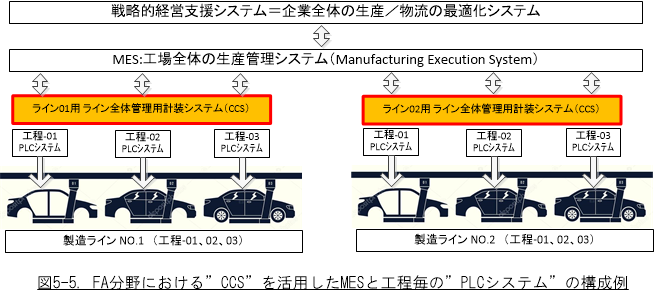